Our service
Third Party Inspection
Third Party Inspection service
Advanced Equipment for Quality Assurance
We possess cutting-edge equipment and comprehensive testing procedures to guarantee the quality of our products. Our array of equipment comprises large digital direct-reading spectrometers, flaw detectors, hydrogen-oxygen-nitrogen analyzers, carbon-sulfur analyzers, servo universal testing machines, low-temperature impact testing machines capable of withstanding -60°C, Zeiss microscopes, and various other specialized equipment. These resources ensure that our products consistently meet the exacting requirements of our customers.
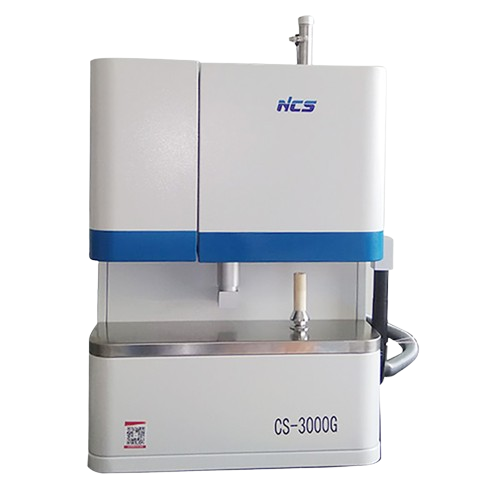
Carbon / Sulfur Analyzer
The CS-2000 analyzer, uniquely capable of determining carbon and sulfur content in both organic and inorganic samples, sets a new standard. Equipped with both induction and resistance furnaces, it covers the full range of carbon and sulfur analysis. Featuring up to four independent infrared cells, the CS-2000 allows precise and simultaneous analysis of varying carbon and sulfur concentrations. Customizable sensitivity through IR-path length selection ensures optimal measurement for each application.
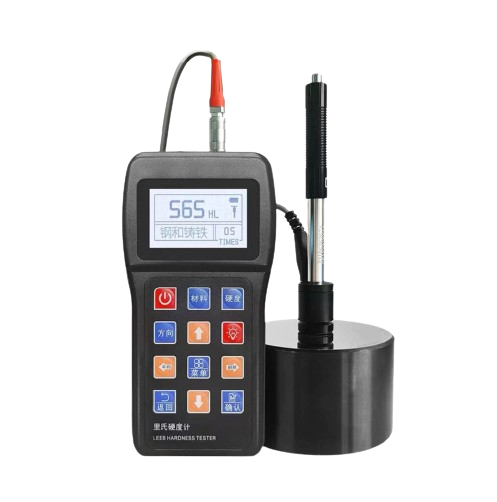
Hardness Test
Hardness testing assesses a sample’s resistance to material deformation under constant compression from a sharp object. These tests rely on measuring critical dimensions of an indentation left by a specific indenter size and load. We perform hardness tests on Rockwell, Vickers, and Brinell scales.
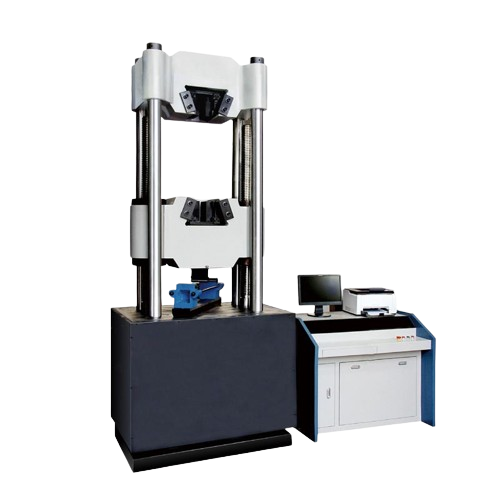
Tensile Test
In a tensile test, a sample undergoes controlled tension until failure. Results are commonly used for material selection, quality control, and predicting material behavior under different forces. Measured properties include ultimate tensile strength, maximum elongation, and reduction in area.
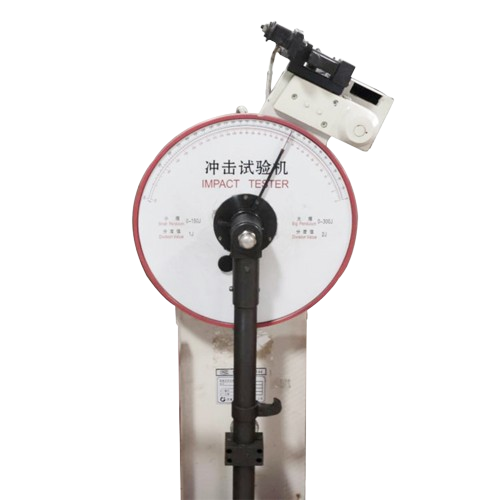
Impact Test
Impact testing evaluates an object’s ability to withstand high-rate loading, often involving high-speed object collisions. A material’s resistance to impact plays a crucial role in part service life and material suitability for specific applications. Impact testing typically employs Charpy and IZOD specimen configurations.
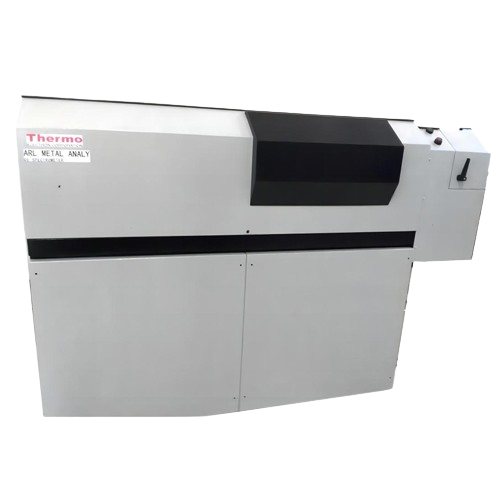
Spectro Test
Leverage our customized steel services. Spectro testing is performed on raw material, forged, and heat-treated batches to ensure compliance with specified chemical composition.
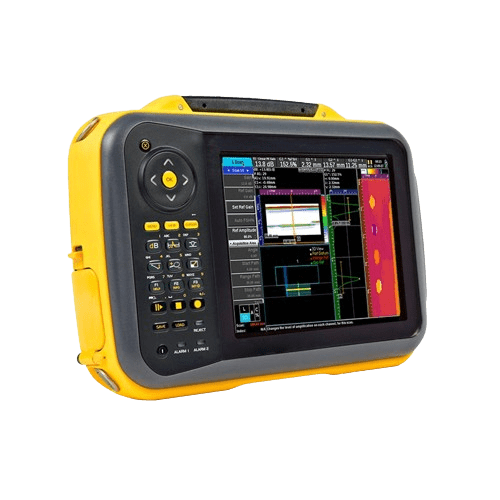
UT Test
Ultrasonic testing (UT) encompasses non-destructive techniques using ultrasonic waves. Common applications involve transmitting short ultrasonic pulse-waves (0.1-15 MHz) into materials to detect internal flaws or characterize materials. Ultrasonic thickness measurement, for instance, monitors pipe corrosion by measuring thickness.