Special Steel 304/304L, often referred to as 18-8 stainless steel due to its chromium and nickel content, reigns supreme as the most ubiquitous and versatile grade in the stainless steel family. But what exactly makes this metal so special? Buckle up, material enthusiasts, as we delve into the world of 304/304L, exploring its composition, properties, applications, and everything in between.
the Compositional Secrets of 304/304L
At the heart of 304/304L lies a carefully orchestrated blend of elements. Let’s peek under the hood and see what makes it tick:
Element | 304 (wt%) | 304L (wt%) | Key Characteristic |
---|---|---|---|
Chromium (Cr) | 18.00-20.00 | 18.00-20.00 | Corrosion resistance champion |
Nickel (Ni) | 8.00-12.00 | 8.00-12.00 | Formability and strength enhancer |
Carbon (C) | Max 0.08 | Max 0.03 | Lower carbon in 304L reduces carbide precipitation, enhancing weldability |
Manganese (Mn) | Max 2.00 | Max 2.00 | Strength and work hardening contributor |
Phosphorus (P) | Max 0.045 | Max 0.045 | Limits grain growth |
Sulfur (S) | Max 0.03 | Max 0.03 | Similar to P, controls grain size |
Silicon (Si) | Max 0.75 | Max 0.75 | Improves oxidation resistance |
Iron (Fe) | Balance | Balance | The foundational element |
As you can see, chromium takes center stage, acting as the primary shield against corrosion. Nickel, the ever-reliable sidekick, bolsters strength and ductility, making 304/304L a dream to work with for various forming processes. The lower carbon content in 304L minimizes the formation of carbides during welding, translating to superior weldability compared to its 304 counterpart.
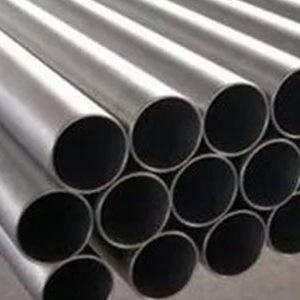
Properties of Special Steel 304/304L
Now that we’ve met the building blocks, let’s explore the resulting properties that have solidified 304/304L’s position as a material superstar:
Property | Description |
---|---|
Corrosion Resistance | The chromium-rich surface layer, known as the passive layer, effectively fends off rust and corrosion in mildly oxidizing environments. Think everyday applications like kitchenware, architectural panels, and automotive trim. |
Formability | The high nickel content grants 304/304L excellent ductility and pliability, making it ideal for deep drawing, stamping, and bending operations. Imagine the intricate shapes possible for sinks, cookware, and appliance components. |
Weldability | The lower carbon content in 304L makes it a champion when it comes to welding. This translates to smooth, strong welds without the worry of excessive carbide formation, a concern for standard 304. |
Strength | While not the strongest steel out there, 304/304L offers a respectable balance of strength and formability. It’s suitable for applications where structural integrity is important but lightweight construction is desired. |
Work Hardening | The ability to become stronger and more rigid through cold working processes like rolling or drawing is another valuable trait of 304/304L. This allows for tailored strength characteristics in specific areas of a component. |
Hygiene | The smooth, non-porous surface of 304/304L resists the growth of bacteria and other microorganisms, making it a hygienic choice for food processing equipment, medical instruments, and pharmaceutical applications. |
Applications of 304/304L
The versatility of 304/304L translates into a vast array of applications across various industries. Here’s a glimpse into its diverse kingdom:
Industry | Application Examples |
---|---|
Construction | Architectural panels, roofing, cladding, railings, fasteners, decorative elements |
Automotive | Exhaust Wheel trims, body panels (especially for non-load-bearing components), exhaust systems |
Food Processing | Tanks, vats, pipelines, utensils, cutlery |
Chemical Processing | Tanks, vessels, piping for handling mild chemicals |
Medical & Pharmaceutical | Surgical instruments, sterilizing equipment, pharmaceutical processing equipment |
Household Appliances | Sinks, refrigerators, dishwashers, washing machines, dryer drums |
Consumer Goods | Cutlery, cookware, beverage containers, hardware |
Think about your kitchen sink – the chances are high it’s crafted from 304/304L. Its ability to withstand daily wear and tear, resist corrosion from water and food acids, and maintain a sleek, hygienic surface makes it the perfect choice. Similarly, architectural panels adorning skyscrapers and shopping malls often leverage the strength, durability, and aesthetic appeal of 304/304L.
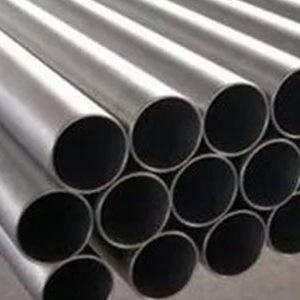
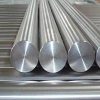
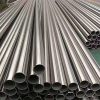
Specific 304/304L Metal Powder Models
Now, let’s delve into the fascinating realm of 3D printing and explore some specific 304/304L metal powder models that are revolutionizing manufacturing:
- AMETEK SMP Eighty Four 304L Stainless Steel Powder – This gas-atomized powder boasts high sphericity and flowability, making it ideal for laser beam melting (LBM) and electron beam melting (EBM) additive manufacturing processes. Its low oxygen content minimizes the risk of porosity in printed parts.
- Sandvik Osprey® 304L – Engineered for a variety of additive manufacturing techniques, including LBM, EBM, cold spray, and metal injection molding (MIM), this powder offers exceptional mechanical properties and corrosion resistance.
- Höganäs 304L – A trusted choice for LBM and EBM, this powder features a narrow particle size distribution, ensuring consistent printing results. Its high tap density allows for efficient packing during the printing process.
- LPW 304L – Certified to meet stringent aerospace industry standards, this gas-atomized powder delivers exceptional strength and ductility for demanding applications.
- Carpenter Additive AM304L – Optimized for LBM and EBM, this powder exhibits excellent printability and post-processing characteristics. Its low inclusion content minimizes the risk of defects in printed parts.
- SLM Solutions SLM® 316L (While not strictly 304L, it’s a close relative) – This gas-atomized powder, similar in composition to 304L with added molybdenum for enhanced corrosion resistance, is specifically designed for SLM (Selective Laser Melting) machines. Its spherical morphology ensures smooth powder flow and high packing density.
- ExOne ExOStrength 316L (Another close relative) – Developed for binder jet additive manufacturing (BJAM), this powder offers good strength and corrosion resistance for applications requiring those properties but not the high nickel content of 304L.
- BASF AM Powder 316L (Yet another close relative) – This gas-atomized powder, similar to SLM Solutions SLM® 316L, caters to SLM processes and boasts excellent flowability and packing density.
- GE Additive Arcam AM316L (Similar to 304L with added molybdenum) – This powder is tailored for EBM machines and delivers exceptional mechanical properties for demanding aerospace and medical applications.
- EOS StainlessSteel 316L V2 (Similar to 304L with added molybdenum) – Optimized for laser melting processes, this powder offers consistent printability and high-quality results.
It’s important to note that while these examples showcase 304L and its close relatives (316L with added molybdenum for enhanced corrosion resistance), the specific powder choice depends on the intended application, desired properties, and the chosen additive manufacturing technology.
the Pros and Cons of 304/304L
No material is perfect, and 304/304L is no exception. Let’s explore its strengths and weaknesses to help you make informed decisions:
Advantages:
- Excellent Corrosion Resistance: As highlighted earlier, 304/304L is a champion against corrosion in mildly oxidizing environments, making it ideal for diverse applications, from kitchenware to architectural cladding.
- Superior Formability: The high nickel content grants 304/304L exceptional pliability, allowing for intricate shapes to be formed through processes like deep drawing and stamping. Imagine the seamless curves of a stainless steel sink or the intricate details of a medical instrument.
- Enhanced Weldability: The lower carbon content in 304L makes it a star performer when it comes to welding. This translates to smooth, strong welds without the worry of excessive carbide formation, a concern for standard 304. This is crucial for applications where a strong, leak-proof connection is paramount.
- Respectable Strength: While not the strongest steel on the market, 304/304L offers a well-balanced combination of strength and formability. This makes it suitable for applications where structural integrity is important but lightweight construction is desired. Think about automotive wheel trims or appliance components.
- Work Hardening: The ability to become stronger and more rigid through cold working processes like rolling or drawing is another valuable asset of 304/304L. This allows for tailored strength characteristics in specific areas of a component, enhancing its performance.
- Hygienic Properties: The smooth, non-porous surface of 304/304L discourages the growth of bacteria and other microorganisms, making it a hygienic choice for food processing equipment, medical instruments, and pharmaceutical applications. This is a critical factor for maintaining cleanliness and preventing contamination.
Disadvantages:
- Limited Corrosion Resistance in Harsh Environments: While impressive in mild conditions, 304/304L can struggle against highly acidic or chloride-rich environments. For applications like marine components or equipment exposed to harsh chemicals, higher-grade stainless steels with increased molybdenum content might be necessary.
- Susceptibility to Pitting Corrosion: Under certain conditions, such as stagnant water containing chlorides, 304/304L is susceptible to a localized form of corrosion called pitting. Careful design considerations and surface treatments can help mitigate this risk.
- Relatively Lower Strength Compared to High-Strength Steels: If an application demands exceptional strength-to-weight ratio, there might be better options. For instance, some high-strength steels can offer significantly more strength without a substantial weight increase.
- Higher Cost Compared to Common Steels: Due to its superior properties, 304/304L typically comes at a higher cost compared to common steels like mild steel. However, its durability, corrosion resistance, and long-term value often justify the initial investment.
- Magnetic Properties: While not highly magnetic, 304/304L exhibits some degree of magnetism. This might be a limitation for applications requiring strictly non-magnetic materials.
By carefully considering the advantages and limitations of 304/304L, you can make informed decisions about its suitability for your specific project requirements.
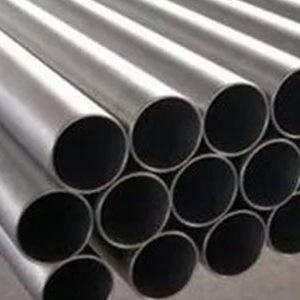
FAQ
Q: What is the difference between 304 and 304L?
A: The key difference lies in the carbon content. 304L boasts a lower carbon content (max 0.03%) compared to 304 (max 0.08%). This seemingly small difference translates to a significant improvement in weldability for 304L due to the reduced formation of carbides during the welding process.
Q: Is 304/304L food safe?
A: Absolutely! The smooth, non-porous surface of 304/304L resists bacteria growth and is considered food-safe by regulatory bodies. This makes it a popular choice for cookware, cutlery, and food processing equipment.
Q: Can 304/304L be used outdoors?
A: In most outdoor environments with mild conditions, 304/304L performs well. However, for areas with high salt spray or harsh chemicals, higher-grade stainless steels with increased molybdenum content might be more suitable for enhanced corrosion resistance.
Q: Is 304/304L magnetic?
A: Yes, 304/304L exhibits some degree of magnetism. While not highly magnetic, this might be a limiting factor for applications requiring strictly non-magnetic materials.
Q: Can 304/304L be 3D printed?
A: Absolutely! 304/304L, particularly the low-carbon variant 304L, is a popular choice for metal additive manufacturing (AM) due to its several advantages:
- Excellent Printability: The spherical morphology of metal powders specifically designed for 3D printing allows for smooth powder flow and efficient packing during the printing process. This translates to high-quality printed parts with minimal defects.
- Good Weldability: As discussed earlier, 304L’s low carbon content makes it weld well. This characteristic is also beneficial in 3D printing, where the material is essentially being “welded” layer by layer.
- Respectable Strength and Formability: The balanced combination of strength and formability of 304/304L makes it suitable for a variety of 3D printed components. Depending on the specific application, the design can be optimized to leverage these properties.
- Corrosion Resistance: While the harsh environments of some 3D printing processes might pose temporary challenges, the inherent corrosion resistance of 304/304L remains a valuable asset for the final printed part.
Here are some additional points to consider for 3D printing with 304/304L:
- Powder Selection: Choosing the right metal powder formulation is crucial. Look for powders specifically designed for the chosen 3D printing technology (e.g., Laser Beam Melting, Electron Beam Melting) and optimized for printability and final part properties.
- Post-Processing: Depending on the application and desired surface finish, post-processing techniques like heat treatment, machining, or polishing might be necessary for 3D printed parts made from 304/304L.
- Design for Additive Manufacturing (DfAM): Taking advantage of the design freedom offered by 3D printing allows for components to be optimized for 304/304L’s properties, potentially leading to lighter, stronger, and more functional parts.
By understanding these factors, you can leverage the strengths of 304/304L to create innovative and functional components through 3D printing.
In conclusion, Special Steel 304/304L stands as a testament to the power of material science. Its unique blend of properties – excellent corrosion resistance, superior formability, good weldability, and a balance of strength and weight – has solidified its position as a cornerstone material across various industries. From the gleaming surfaces of kitchen appliances to the intricate structures of medical instruments, 304/304L continues to shape our world in countless ways. As 3D printing technology evolves, 304/304L is poised to play a vital role in the future of manufacturing, enabling the creation of complex and innovative components.